- Within modern construction projects, particularly large-scale developments, BIM supports greater precision, quality and efficiency in precast manufacturing, which helps companies meet the required demands for precision and speed.
- Traditional precast construction techniques struggle with issues, including accuracy, coordination problems, material waste and inefficiencies within project management. This leads to reworks and delays.
- This case study walkthrough illustrates how BIM with capabilities like clash detection, rebar detailing, and real-time monitoring enables a seamless, cost-effective, and clash-free precast production process.
Table of Contents
- The Importance of Precision in Precast Manufacturing
- Step 1: Understanding the Client’s Vision and Challenges
- Step 2: Creating the Digital Twin – 3D BIM Modeling Beyond Visualization
- Step 3: Rebar Detailing and Shop Drawings – Transitioning from Digital to Physical
- Step 4: Comprehensive Clash Detection – Minimizing Errors and Ensuring Precision
- Step 5: Optimizing Production through Material Scheduling and Real-Time Tracking
- Final Outcome and Lasting Impact: A New Standard for Efficiency and Quality
- Key Takeaways: The Long-Term Value of BIM in Precast Manufacturing
- Conclusion
The Importance of Precision in Precast Manufacturing
Within design and construction, the role of precast manufacturing has gained substantial momentum in regions, including the UAE, where large-scale infrastructure is common. Precast components like beams, walls, and columns support faster project “turnaround times (TAT)” and improved structural integrity, which requires a greater level of accuracy, on-site precision, and seamless assembly. For one UAE-based precast manufacturer, the need to manage a project of over 15,000 unique precast components presented significant obstacles. These challenges were beyond those of routine production, as they included ensuring greater structural performance, reducing material waste and watertight coordination between various project participants.
The following walkthrough illustrates how HitechDigital partnered with the client to generate a coordinated and clash-free 3D BIM precast model at LOD 450. By detailing the collaborative process, clash detection tools, and scheduling efficiencies driven by the team, we’ll show how, during each phase, BIM capabilities helped realize the new digital construction standards.
Step 1: Understanding the Client’s Vision and Challenges
The project began with an in-depth consultation phase in which HitechDigital’s team sought to fully understand the client’s goals and pain points. As the client’s project requirements were stringent, the production of over 15,000 structural elements required high accuracy, effective management of logistical challenges and inter-team coordination. This scale and complexity meant that traditional methods would fall short, especially given the tight deadlines and need for precision at every stage of the process.
The production of 15,000 structural elements required tolerances of 2 mm to 5 mm with an LOD of 450, backed by rebar connections. The challenges also included coordination with various designers from remote locations for design changes, a long list of precast deliverables within a shorter TAT, and ensuring mitigation of material waste with sequential erection.
The initial phase identified two primary challenges:
1. Complex Rebar Detailing: Precast manufacturing depends on accurate rebar configurations, as these components deliver the structural strength required to withstand bearing loads. Ensuring rebar details aligned with project specifications without on-site modifications was vital.
2. Coordination and Clash Management: With multiple teams working on a project, managing interferences between structural components in the early design phase was necessary to avoid costly rework and production issues.
Solution Initiation: A Model Tailored to Complex Needs
Understanding these obstacles, HitechDigital assembled a specialized team of project engineers and BIM modelers with expertise in precast manufacturing, structural detailing and large-scale project management. Our strategy was centered on building a fully integrated 3D precast model using Revit for model creation and BIM360 for real-time data sharing and error reduction.
To meet the project’s complexity, we built a 3D precast model at Level of Detail (LOD) 450, a standard that sets specific details for every element that is suitable for fabrication.
A specific LOD not only enabled the team to visualize the project’s structural components but also to simulate assembly and ensure precise fitment. This higher level of detail helped the client virtually build the structure before actual production commenced. This helped to identify and address potential problems that could arise later.
Step 2: Creating the Digital Twin – 3D BIM Modeling Beyond Visualization
The 3D BIM precast model built for this project proved to be more than a visualization tool. In line with LOD 450 standards, each component within the model was made to work as a digital twin of the real-world counterpart, including details down to the elemental level. For example, each precast column, wall panel, and beam within the model had information regarding dimensions, rebar configurations, assembly instructions, and material types. The Object-Based Modeling phase enabled the team and client to quickly implement early design changes, enhancing model optimization.
Generating such an accurate model requires a phased workflow. The first phase involved the development of primary structural elements to build the foundational framework. From there, HitechDigital built secondary elements and introduced various details layer by layer. Each phase was cross verified for potential interferences with existing elements that ensures alignment with real-world conditions.
This phase-by-phase build allows teams to add complexity to the 3D model while maintaining control over every layer’s accuracy and relevance. The 3D models’ high performance and adaptability to project geometry supported the client’s precast production and on-site teams by utilizing a single source of truth for structural assembly.
Step 3: Rebar Detailing and Shop Drawings – Transitioning from Digital to Physical
The rebar detailing element proved to be crucial for project success. Precast manufacturing requires precise rebar layouts, which need to be followed to manage structural integrity. HitechDigital’s team carefully built each rebar placement, configuration and size using the 3D precast model as a benchmark for detailed and millimeter-specific shop drawings.
Shop drawings were shared with various teams through BIM360, which provided real-time updates and feedback loops. This helped us to stay consistent, as modifications were made to align design changes with rebar details. By incorporating extensive detailing, HitechDigital enabled a seamless transition from design to fabrication, facilitating a reduction in assembly schedules, material waste, and labor costs on site.
Moreover, each component’s rebar configuration within the model was verified through interference detection before fabrication began. This eliminated potential problems that could disrupt project schedules and expensive reworks.
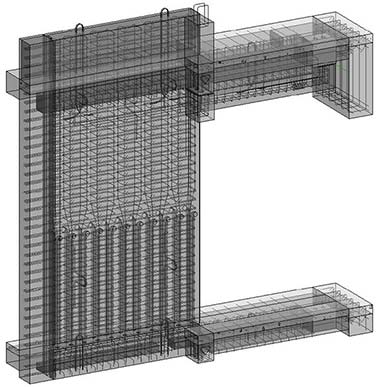
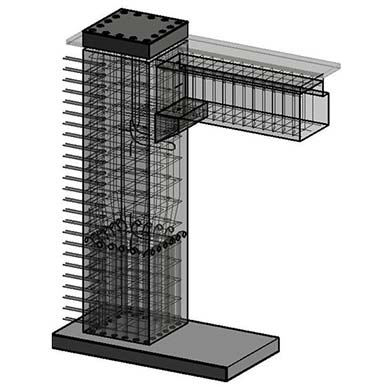
Step 4: Comprehensive Clash Detection – Minimizing Errors and Ensuring Precision
Clash detection was thorough to ensure every structural element fit accurately without any interference from other components. HitechDigital’s strategy for clash detection was continuous and preemptive. Rather than waiting until the 3D precast model was developed to conduct clash checks, the team deployed a series of unique clash detection tests at every design stage. As new elements were included within the model, the software flagged potential issues, allowing the team to modify designs and manage accuracy in real time.
This clash detection approach not only lowered the risk of rework once the precast components were delivered but also helped the client identify issues in the preconstruction stage. By using tools within Autodesk Revit and BIM360, the team at HitechDigital set protocols to handle and rectify clashes, promoting coordinated design for greater production accuracy and lower on-site disruptions.
The clash-free model was integral to supporting the client’s zero-waste policy. With a coordinated design in place, HitechDigital was able to provide highly accurate material estimates, which allowed the client to optimize resource allocation and reduce costs associated with excess material.
Step 5: Optimizing Production through Material Scheduling and Real-Time Tracking
In addition to creating a 3D precast model that met structural needs, we built the model using an embedded scheduling system tailored to a unique workflow.
This capability allowed the client to monitor the project’s progression in real time, from resource allocation to final installation. The team integrated real-time tracking for every component, enabling accurate, dynamic production management and assembly schedules.
Comprehensive BBS with exact lengths, quantities, bend shapes, and angles, along with images and 3D views, were produced.
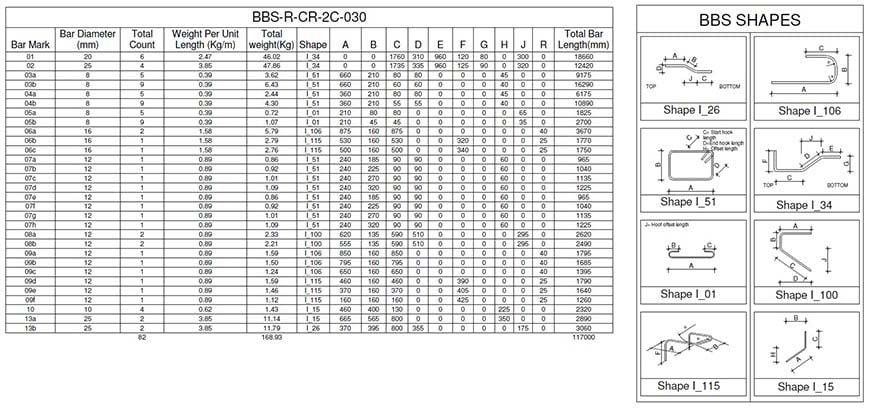
With scheduling customized for each phase, the client’s team could project accurate material quantities, ensuring efficient resource utilization and just-in-time delivery. The client witnessed a considerable reduction in waste, as he could predict material needs and avoid overproduction. According to post-project reports, these scheduling improvements contributed to a significant reduction in project costs through minimal on-site clashes, lower reworks, and precise material estimates.
Final Outcome and Lasting Impact: A New Standard for Efficiency and Quality
The project concluded with an accurate and information-rich 3D BIM precast model that served as a long-term and valuable asset for the client. This in-depth digital model provided a reliable deliverable for the project, enabling the client’s team to visualize, track and monitor the progress of elements at any time. With BIM, the client successfully met production targets and managed on-site schedules that would not have been achievable using legacy methods.
More than meeting project requirements, the client experienced a shift in workflow. They found that the clash-free and detailed model enhanced their belief in BIM as a production tool, proving that digital construction could deliver high quality and efficiency. This project marked a turning point for the client, as they deployed BIM as a core tool and established HitechDigital’s approach as a standard for future projects.
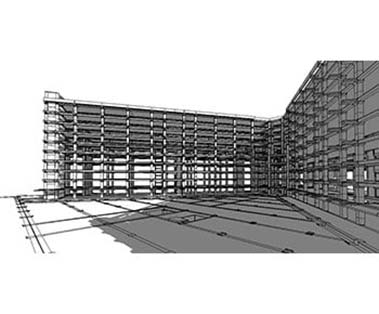
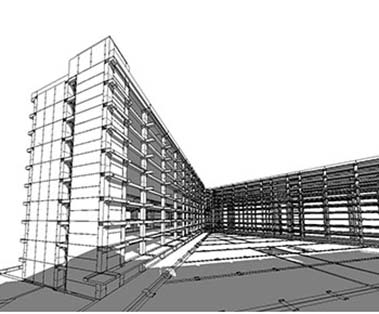
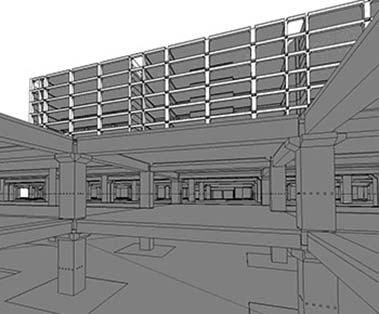
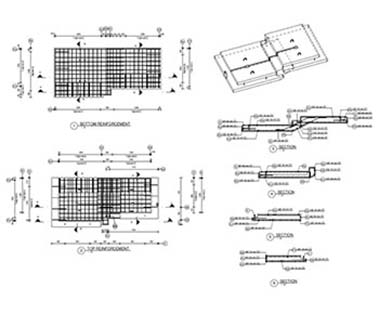
Key Takeaways: The Long-Term Value of BIM in Precast Manufacturing
Quality
Enhanced quality of precast deliverables.
Cost
Accurate procurement facilitated by 3D models with precision under 5mm for M60-grade concrete, achieving zero material waste.
Cost Savings
Achieved through 100% accuracy in deliverables.
Time
Rapid turnaround time (TAT) for BIM deliverables within 6-8 months, enabling faster on-site building erection.
Conclusion
This case study demonstrates how advanced BIM detailing helps precast manufacturing and establishes new benchmarks in precision, efficiency and collaboration.
By implementing a comprehensive 3D modeling approach with 5 mm accuracy at LOD 450, we transformed a complex 15,000-component project into a seamless digital-to-physical workflow. The results speak volumes: zero clashes, minimal waste, optimized production scheduling and significantly reduced TAT.
Beyond immediate project success, this implementation has fundamentally altered our client’s work process, establishing BIM as their core production methodology moving forward. The real triumph lies not just in solving present challenges, but in creating a sustainable framework for future projects that demands less rework, enables better resource allocation, and supports more precise construction outcomes.
As construction technology evolves, this approach represents the future of precast manufacturing—where digital precision drives physical perfection.
Transform precast manufacturing with custom BIM detailing.
Leverage accuracy, efficiency, and expedited project handovers today!