- Automation in MEP BIM quality control ensures adherence to geometric specifications, codes, and constructability requirements.
- It allows for clash detection and resolution, data integrity and metadata validation, and intelligent rule-based checks.
- Automation helps to mitigate errors through embedded rules, real-time error detection and proactive alerts.
Table of Contents
Automation in MEP BIM modeling enhances precision and coordination while streamlining quality control processes, and reducing errors and inefficiencies in building design and construction.
Quality control in mechanical, electrical and plumbing (MEP) systems is instrumental in ensuring the structural integrity and functionality of any building design. However, with construction projects becoming increasingly complex due to the intricate interdependencies between mechanical, electrical and plumbing systems, manual quality control methods are falling short in managing these sophisticated design challenges.
Building Information Modeling (BIM) has modernized our approach toward construction design by providing digital representations that enable MEP consultants to get a richer understanding of building systems through visualization.
Automation with BIM takes the process a step further by leveraging algorithms and data analytics to overcome the limitations of traditional quality control methodologies. It enables precise, comprehensive design validation that goes beyond human capabilities.
Consultants offering MEP BIM Modeling services leverage automation to accelerate QC processes while maintaining accuracy and precision.
Understanding MEP BIM quality control
MEP BIM quality control is a holistic approach to MEP design validation. Its purpose is to ensure that component installations are not only precise, but also optimized for maximum functionality, safety and constructability.
While traditional quality control methods involve manual checks and human expertise, automating quality checks in MEP BIM models provides a multi-dimensional validation approach to address critical design parameters. These advanced procedures include automated checks for geometric accuracy, compliance with codes, clash detection, data validation and constructability reviews. Let’s understand these QC processes in detail.
Types of quality control in MEP BIM models
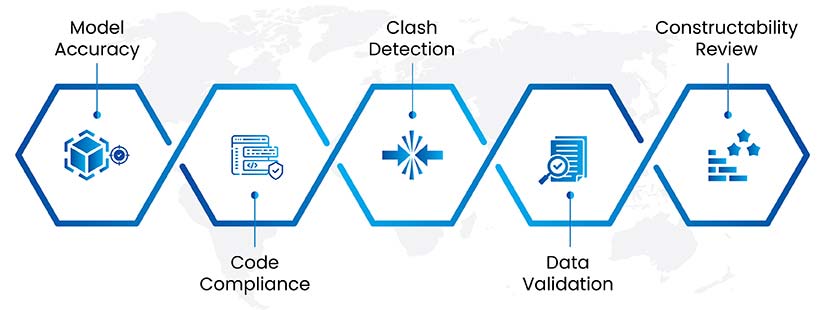
- Model Accuracy: Model accuracy ensures the precise placement, dimensioning and alignment of MEP components within the BIM environment, accounting for precise spatial relationships and system interactions.
- Code Compliance: With code compliance, the risk of regulatory violations can be reduced by validating designs against evolving industry standards and building regulations.
- Clash Detection: This QC process automatically identifies and resolves spatial conflicts between MEP systems and building elements to prevent potential construction challenges.
- Data Validation: Through data validation, the accuracy and completeness of the model metadata can be confirmed while ensuring correct attributes for installation, maintenance and long-term performance.
- Constructability Review: Finally, a constructability review involves making a practical implementation assessment of the designs to verify efficient construction methods and suggest potential optimization opportunities.
Challenges with manual quality control
Ensuring a rigorous quality control standard in MEP BIM models using a manual approach comes with a whole set of challenges. These hurdles arise from two main factors: the inherent complexities in MEP systems and the demanding nature of construction projects. Some key challenges include:
Complexity of MEP Systems
MEP systems rely largely on accurate architectural and structural models. Any inaccuracies or changes in these foundational models can be reflected in all MEP designs, leading to rippling inconsistencies. For instance, HVAC ducts often share spatial zones with electrical conduits and plumbing lines. Improper coordination results in overlaps, leading to clashes that compromise the system’s functionality and efficiency.
Manual Checking Limitations
Manual quality control methods also struggle to keep up with the growing complexity of MEP designs. Since these designs are highly detailed, with multiple components requiring precise coordination, identifying inconsistencies through the manual approach is not only labor intensive but also error prone.
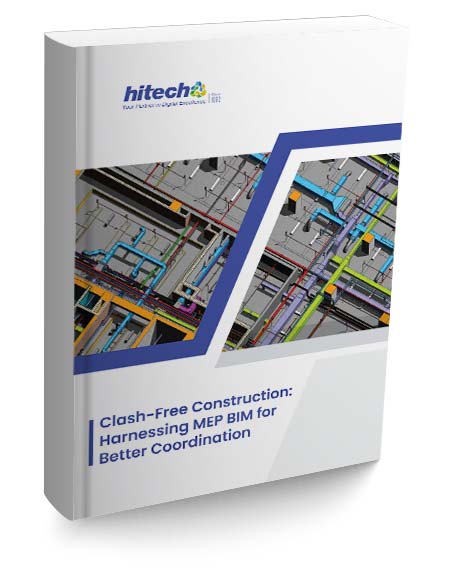
Clash-Free Construction: Harnessing MEP BIM for Better Coordination
- Enhanced collaboration: Facilitates seamless communication and clarity among project participants.
- Clash detection: Identifies MEP interferences early, streamlining workflows and schedules.
- Reduced waste and rework: Enables prefabrication and modular construction, minimizing material waste and on-site rework for sustainability.
The role of automation in MEP BIM quality control
Automation has a significant impact on tackling the challenges of quality control in MEP BIM models. Automated processes can manage extensive datasets by methodically implementing rules and algorithms, conducting complex validations, and reducing dependence on manual procedures.
Here is a thorough examination of how automation improves MEP BIM quality assurance.
Automated validation in MEP systems
By utilizing automation, MEP consultants can ensure that every element in the model adheres to the correct geometric specifications and is coordinated with the overall design. For instance:
- HVAC Systems: Automation checks for proper clearance zones to prevent duct conflicts with structural elements or other MEP systems.
- Electrical Conduits: With automated scripts, consultants can validate the routing of conduits to avoid unnecessary bends or overlaps with plumbing.
With the help of Revit’s Dynamo, automated scripts can detect misaligned ducts or pipes and mark them for correction, greatly cutting down on manual validation time.
Clash detection and resolution
Clash detection stands out as one of the most notable applications of automation in MEP BIM. Automated algorithms can detect spatial conflicts between systems, including plumbing and electrical conduits, using tools like Navisworks. The system identifies conflicts and prioritizes them according to their severity or phase of construction.
A real-time conflict detection feature in Navisworks enables teams to address issues collectively during design sessions, avoiding expensive modifications on-site.
Data integrity and metadata validation
Data parameters like flow rates, power capacities, and material specifications are essential in MEP models. Automation verifies the correctness and completeness of this metadata to ensure that each element complies with project requirements and industry norms.
Utilizing a preset library, Dynamo scripts can compare equipment specifications in the model and identify inconsistencies for examination.
Intelligent rule-based checks
Automation can also facilitate rule-driven systems that eliminate errors in the model development process. These regulations can be integrated directly into BIM tools to uphold design limitations and adherence.
For instance, a rule can ensure that fire sprinkler systems maintain the required clearances from structural beams and prevent code violations during setup.
Simulation and performance analysis
An advanced automation strategy may also involve integrating simulation tools to analyze system performance. For instance:
- Thermal Simulations: Automation evaluates HVAC performance, ensuring proper airflow and temperature regulation.
- Energy Simulations: Automated tools can also calculate the energy efficiency of electrical systems, helping teams optimize designs for sustainability.
With Computational Fluid Dynamics (CFD) simulations, it is possible to streamline BIM integrations and deliver immediate insights into HVAC efficiency, allowing for modifications prior to building.
Real-time error detection and feedback
Automated systems can also be useful in identifying errors as they occur during the model development process. This enables immediate feedback to prevent minor errors from escalating into bigger problems.
A common example could be using a Revit plugin to alert designers when they try to lay a pipe in a restricted area, ensuring immediate compliance.
Automation-driven reporting and collaboration
The integration of AI and machine learning enhances automation by enabling predictive quality control. These systems evaluate past data to forecast possible design problems and recommend solutions.
AI-powered tools can recognize trends in repeated disputes and suggest modifications to avert comparable conflicts in upcoming designs.
Benefits of MEP BIM automation in quality control
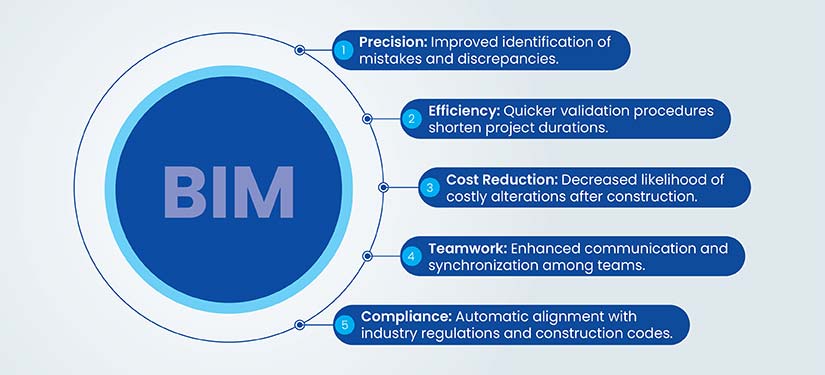
Challenges in MEP BIM quality control
Although there are various advantages, executing quality control in MEP BIM models presents specific challenges. These challenges typically stem from the intrinsic intricacy of MEP systems and the rigorous requirements of construction projects. Let’s discuss some of the prominent challenges in detail.
Complexity of MEP systems
As discussed, MEP systems are intrinsically complex because of their interdisciplinary characteristics. These systems must achieve seamless integration not only among themselves but also with the building’s architectural and structural frameworks.
Intersection of various disciplines
HVAC ducts and other mechanical systems frequently share spatial areas with electrical wires and plumbing pipes. Lack of proper coordination can create overlaps that result in conflicts, potentially undermining the system’s functionality and efficiency.
For instance, while designing a commercial structure, if the path of an HVAC system clashes with plumbing risers because of spatial interference, it can take weeks to resolve the issues manually. Such delays would eventually extend the project deadline. In this scenario, automation can detect and resolve these conflicts sooner.
Collaborating with an experienced HVAC BIM services partner also help ensure that these automated clash detection and resolution processes are implemented effectively, streamlining the workflow and enhancing the quality of the MEP BIM model.
Dependence on architectural and structural models
MEP systems depend significantly on precise architectural and structural models. Any errors or alterations in these fundamental models can create ripples in MEP designs, resulting in discrepancies.
High data volume
The vast volume of data contained in MEP BIM models poses another major challenge. Every component, including pipes, ducts and electrical panels, has linked metadata, which includes dimensions, material details and performance specifications.
Dealing with these large and intricate datasets through manual checks is susceptible to human mistakes and omissions. In many extensive projects, complexity increases, and even a small error can trigger a series of issues throughout the entire MEP BIM model.
Consider a scenario in which there are inconsistencies in metadata for plumbing fixtures in a hospital project. These discrepancies would postpone installations, since the MEP team would need to manually fix every item. Automated validation might have identified these errors weeks in advance, conserving time and resources.
Manual checking limitations
MEP designs contain numerous elements that necessitate exact coordination. Hand-spotting discrepancies in such designs is time-consuming and prone to mistakes.
Consider the case of a multi-story shopping center that necessitates comprehensive MEP collaboration. If manual inspections overlook multiple vertical pipe conflicts with structural components, this can lead to expensive rework.
Evolving standards
Building codes and industry standards are regularly revised to incorporate new technologies, safety measures and environmental factors.
Therefore, designers and quality assurance teams must verify that MEP systems adhere to the most recent codes. This is especially difficult for large-scale initiatives that cover various jurisdictions and may include conflicting requirements.
Automation can simplify this process by cross-referencing the design with updated codes in real time.
Reducing errors in MEP BIM models with automation
Automation in MEP BIM modeling is crucial for minimizing errors and guaranteeing that designs are precise, compliant and optimized for effective installation. Through smart rules, immediate feedback systems, and enhanced validation procedures, automation tackles frequent error sources and reduces discrepancies.
Strategies for error reduction
1. Embedding Rules and Parameters
One of the most effective ways to prevent design inconsistencies is by embedding predefined rules and parameters into the BIM model. These rules enforce constraints and standards, ensuring that designs remain within acceptable limits.
- Rule-Based Design Constraints: Automation allows for the creation of rules that govern system layouts, clearances and placements. For example:
- Minimum clearance zones can be defined around HVAC systems to avoid conflicts with electrical conduits or plumbing pipes.
- Routing constraints for electrical wiring can ensure compliance with safety standards.
- Code Compliance Integration: Rules can also be programed to align with local building codes. As designers create or modify components, the model automatically validates compliance.
2. Real-Time Error Detection
Automation enables real-time monitoring and error detection during model creation. As designers work within the BIM environment, automated tools provide immediate feedback, identifying potential issues before they propagate through the design.
- Dynamic Clash Detection: Automated scripts can constantly study the model for clashes and inconsistencies, as new elements are added or existing ones are adjusted.
- Proactive Alerts: Automation flags noncompliant designs, such as improperly sized ducts or plumbing layouts that exceed pressure limitations, enabling immediate corrections.
Clash-Free MEP Models for a Commercial Project in the USA
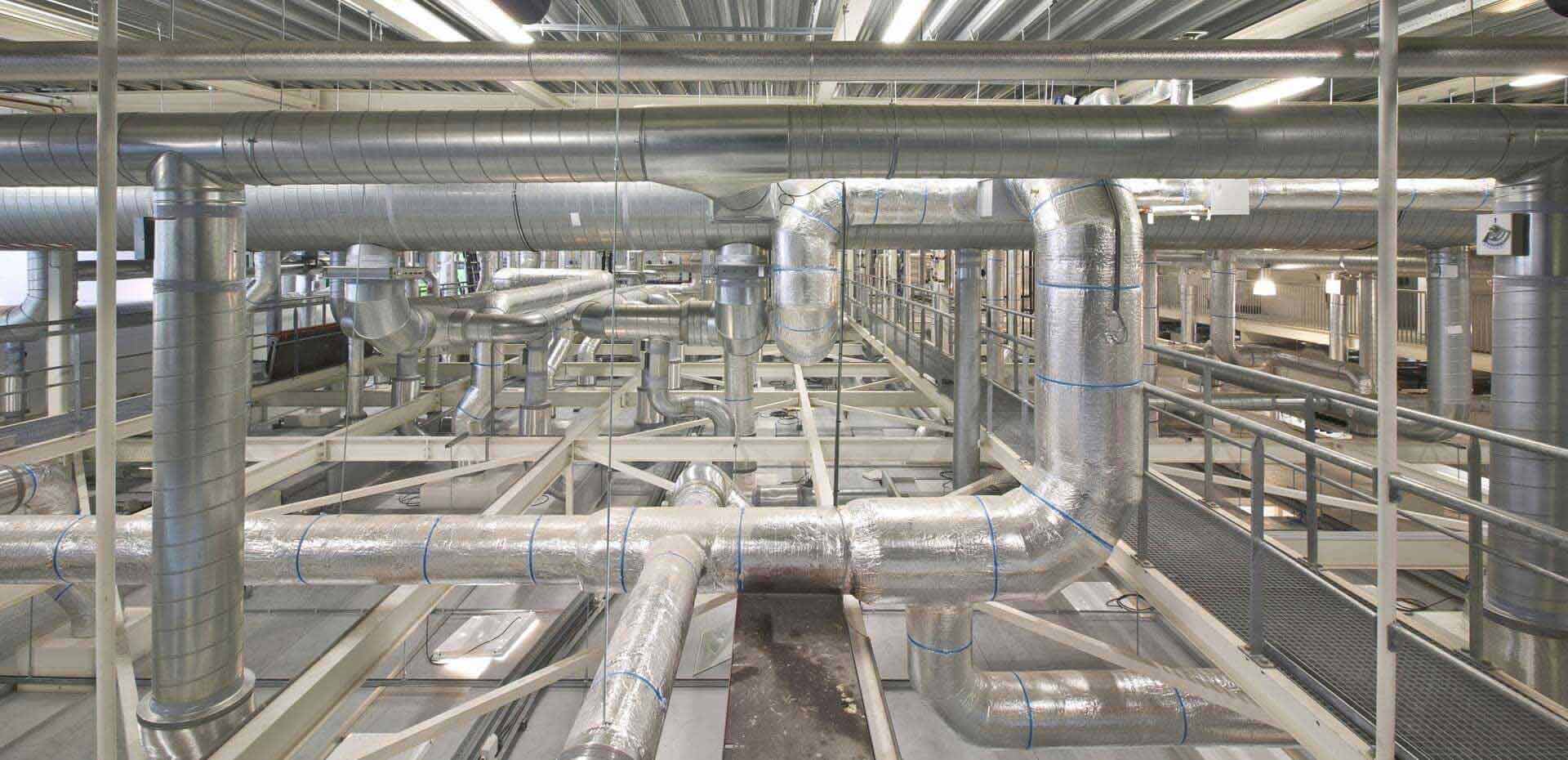
A US-based MEP consultant needed a 360-degree visualization of electrical, plumbing and ventilation systems at the pre-construction stage of a commercial project. They needed a fully coordinated 3D MEP BIM model to ensure accurate component and error-free installation.
HitechDigital provided a coordinated and clash-free 3D MEP model for Mechanical, Electrical and Plumbing disciplines using Revit and Navisworks. Additionally, detailed drawings for electrical, ventilation and plumbing systems were created to ensure accurate spatial coordination, precise components, and hassle-free installation.
Read full Case Study »Future of automation in MEP BIM quality control
The roles of AI and ML are expanding in automating and enhancing quality control in MEP BIM models. These technologies can easily identify patterns by analysing vast datasets and help predict potential issues before they spring up in the construction phase. This proactive approach not only allows teams to address problems early, but also reduces costly reworks and project delays.
Minimize errors with automated BIM MEP clash detection services.
Ensure flawless project designs with our smart tools.